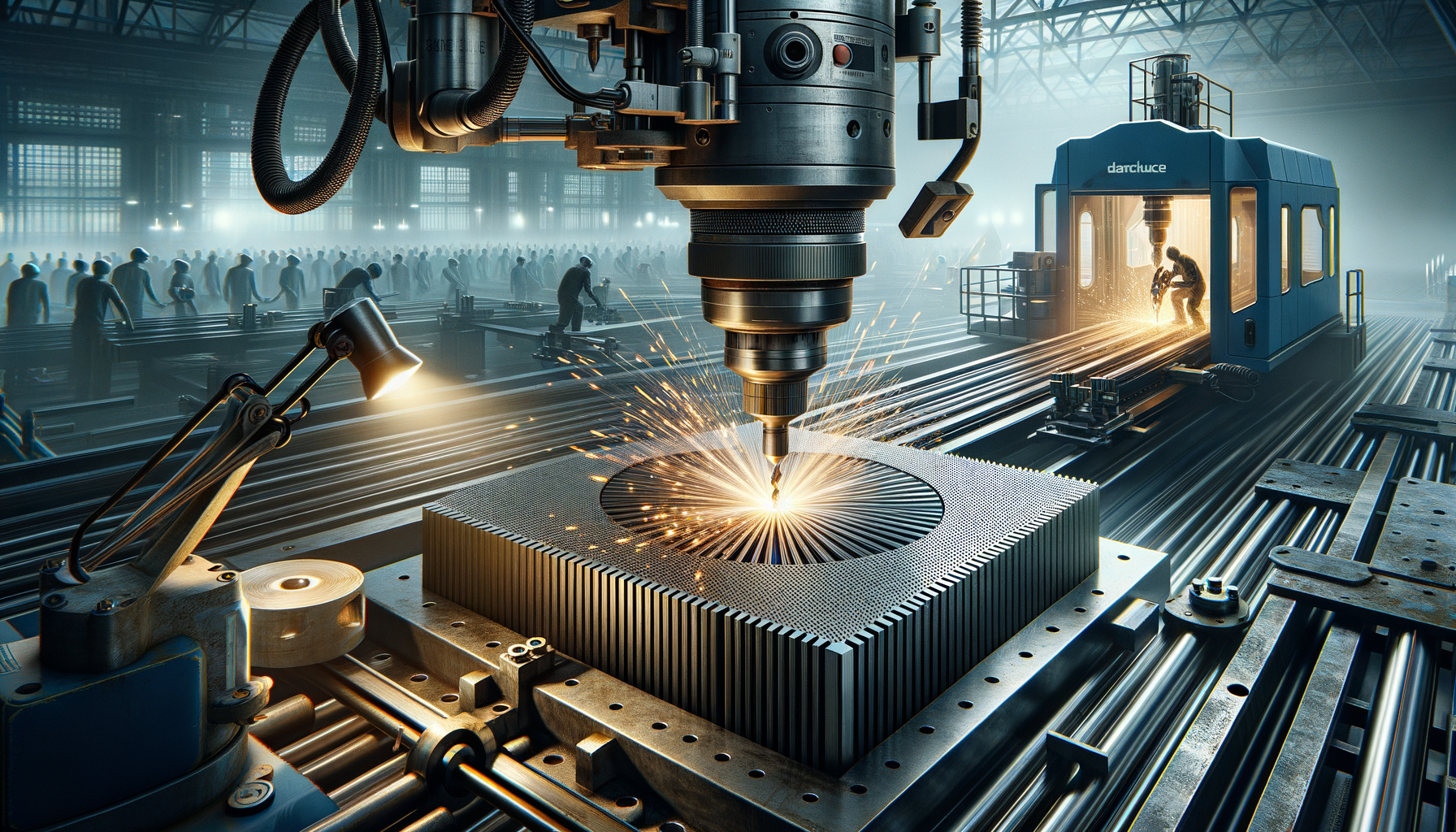
Precision and Power: Exploring Core Drilling Machines and Laser Cutting Technology
Understanding Core Drilling Machines
Core drilling machines are indispensable in various sectors, offering precision and efficiency in extracting cylindrical samples from hard surfaces. Typically used in construction, geology, and material testing, these machines allow for detailed analysis and modifications. The core drilling process involves a rotating drill bit, often diamond-tipped, which cuts through materials like concrete, asphalt, and rock. This method is preferred for its ability to produce clean and accurate cores, essential for assessing the structural integrity of buildings, roads, and other structures.
When selecting a core drilling machine, several factors should be considered. The power source is crucial; machines can be powered by electricity, hydraulics, or pneumatics, each offering different levels of portability and power. Additionally, the drill bit size and material are vital, as they determine the machine’s capability to handle specific tasks. Durability and ease of maintenance are also important, as these machines often operate in challenging environments.
Core drilling machines have evolved significantly, incorporating advanced technologies to enhance performance. Features such as automatic feed systems, digital displays, and variable speed controls have improved precision and user experience. These advancements not only increase efficiency but also ensure safety, reducing the risk of accidents during operation.
The Art of Laser Cutting
Laser cutting technology has revolutionized the manufacturing and fabrication industries, offering unparalleled precision and versatility. This process uses a high-powered laser beam to cut materials, ranging from metals to plastics, with exceptional accuracy. The laser’s ability to produce intricate designs and clean edges makes it a preferred choice for industries such as automotive, aerospace, and electronics.
Laser cutting operates on the principle of focusing a laser beam onto a material, causing it to melt, burn, or vaporize along a precise path. The process is controlled by computer numerical control (CNC) systems, ensuring consistent and repeatable results. This precision is particularly beneficial for producing complex shapes and patterns that would be difficult to achieve with traditional cutting methods.
One of the key advantages of laser cutting is its ability to work with a wide range of materials and thicknesses. From delicate paper to thick steel plates, laser cutters can handle diverse tasks with ease. Moreover, the non-contact nature of the process minimizes material distortion and wastage, making it a cost-effective solution for many applications.
Comparing Core Drilling and Laser Cutting
While core drilling and laser cutting serve different purposes, comparing their functionalities can provide insights into their respective advantages. Core drilling is primarily used for extracting samples or creating holes in hard materials, whereas laser cutting focuses on precision slicing and shaping of materials.
Core drilling is ideal for applications requiring deep penetration into materials, such as creating openings for pipes or cables in construction projects. It is particularly useful in environments where precision is needed to avoid compromising structural integrity. On the other hand, laser cutting excels in scenarios where detailed and intricate designs are necessary, such as in custom fabrication and prototyping.
Both technologies offer unique benefits, with core drilling providing depth and strength, while laser cutting delivers precision and versatility. Understanding these differences is crucial for industries to choose the appropriate technology based on their specific needs and objectives.
Applications and Innovations
The applications of core drilling machines and laser cutting technology are vast and continually expanding. In construction, core drilling is essential for creating openings for utilities and testing material strength. It is also used in geological surveys to extract rock samples for analysis. Innovations in core drilling include the development of more efficient drill bits and automated systems that enhance precision and reduce labor costs.
Laser cutting, meanwhile, has found applications in diverse fields such as automotive manufacturing, where it is used to cut intricate parts with high precision. The technology is also prevalent in the fashion industry for cutting fabrics and creating detailed patterns. Recent innovations in laser cutting include fiber lasers, which offer faster cutting speeds and improved energy efficiency compared to traditional CO2 lasers.
Both technologies continue to evolve, driven by the demand for higher efficiency and precision. As industries strive to improve productivity and reduce environmental impact, advancements in core drilling and laser cutting will play a significant role in shaping the future of manufacturing and construction.
Conclusion: Choosing the Right Technology
In conclusion, both core drilling machines and laser cutting technology offer distinct advantages and are essential tools in their respective fields. Core drilling is unmatched in its ability to penetrate hard materials and extract samples, making it invaluable in construction and geology. Laser cutting, with its precision and versatility, is a cornerstone in manufacturing and fabrication industries.
When choosing between these technologies, it is important to consider the specific requirements of your project. Factors such as material type, desired precision, and application purpose should guide your decision. By understanding the strengths and limitations of each technology, industries can optimize their processes and achieve superior results.
As both technologies continue to advance, they will undoubtedly open new possibilities and applications, driving innovation and efficiency across multiple sectors.